In Case You Missed It: Inspection Masterclass Recap
Industry experts:
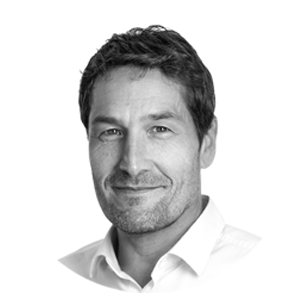
Raal Harris
Ocean Technologies Group
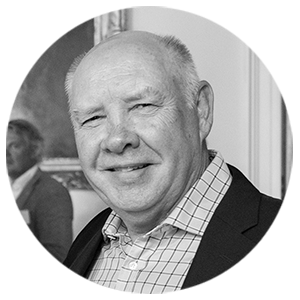
Andy Easdown
Ocean Technologies Group
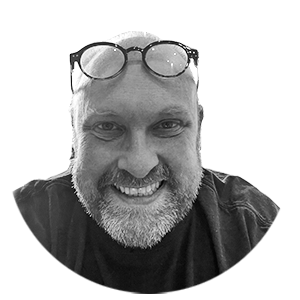
Hadyn Abbey
Cambridge Maritime
Inspections are crucial for ensuring safety and compliance in operations. They come in various forms, including regulatory, internal, and third-party inspections, each with its own focus and requirements. To successfully navigate these inspections, preparation is key.
This article, containing expert insights from our recent inspection excellence webinar, outlines the essential steps for effective inspection preparation.
Key Steps for Vessel Inspection Preparation:
-
Crew Briefings: Ensure the crew understands their roles and responsibilities during an inspection.
-
First Impressions: Maintain cleanliness and organisation to make a positive impression on inspectors.
-
Communication: Be ready to engage transparently and cooperatively with inspectors.
-
Equipment Checks: Inspect and maintain equipment ahead of time to identify potential issues and put plans in place to rectify them.
-
Training for Inspections: Conduct regular training sessions and drills to improve the crew’s knowledge and response during inspections.
-
Simulated Mock Inspections: Use mock inspections to simulate real inspection scenarios, helping the crew practice their responses.
-
Documentation: Have all necessary documents organised and up to date. This includes logs, certificates, and records.
Crew Briefings:
Crew briefings are fundamental in equipping each team member with the knowledge and confidence required for an inspection. These sessions are pivotal for disseminating information and ensuring that everyone aboard understands their individual roles and responsibilities. The essence of effective briefings lies in their ability to translate the complex requirements of an inspection into clear, actionable tasks for each crew member.
By focusing on direct communication and engagement, these briefings help to make the inspection process easier to understand. It is not just about instructing crew members on what to do; but it’s about creating an interactive learning environment where questions are encouraged, leading to a better understanding of what is expected during an inspection. Simulating inspection scenarios can further improve the effectiveness of these briefings, providing crew members with practical experience in handling inquiries and demonstrating compliance confidently.
Incorporating feedback from previous inspections into these briefings can also offer valuable learning opportunities for crew members, highlighting areas for improvement and reinforcing best practices.
“Be succinct. Only answer the question that’s asked.
Don’t tell the inspector information you think they should know, but just answer the question. Otherwise, you could dig yourself into a pit that you really don’t want to. Answer the question succinctly. We’ll ask a question; you’ll answer and then we’ll just ask for evidence and then move on.”
– Hadyn Abbey
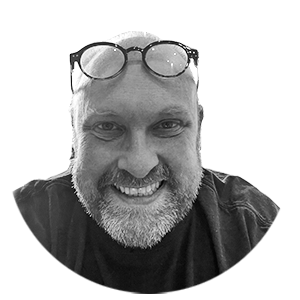
First Impressions:
First impressions matter a lot in inspections. How clean and organised a ship looks can tell an inspector a lot before they even start checking anything formally.
Keeping the ship clean and organised is a job for everyone on board, not just a few people. Making sure everyone cares about their workspace helps here, with them knowing it reflects on their professionalism. Having regular cleaning routines, clear signage, and organised storage means everything is where it should be, even if an inspector turns up at short notice.
When everyone on the crew is involved in keeping the ship in good shape, it builds a sense of pride and shared responsibility. Everyone has a part to play. Training that includes how to keep things clean and organised helps make these habits a natural part of the crew’s routine.
The effort to keep the ship looking its best makes a good first impression and demonstrates the crew’s hard work and respect for their vessel. Inspectors notice this effort and start their inspections positively, knowing they’re dealing with a team that aims for excellence. The way a ship looks at first glance can really affect how the rest of the inspection goes, making it more likely to be positive.
“As soon as you go on board, you look at how the crew are they presenting themselves. Right from the gangway or accommodation ladder to the accommodation.
Are you challenged at the top of the accommodation? Is the ISPS code being followed? Are they following their own processes?”
– Hadyn Abbey
Communication:
Clear and honest communication with inspectors is vital. Being open and working together with inspectors can make the inspection process smoother for everyone involved. This means being upfront about any issues and not hiding any problems, transparency leads to inspectors becoming more trusting and a more constructive inspection.
When talking to inspectors, it’s important to listen carefully and respond accurately to their questions. Providing detailed and clear answers shows that the crew understands their roles and the ship’s operations. An effective strategy is to respond to inspectors’ queries with precision, avoiding unnecessary details that might complicate the conversation. This approach helps in keeping the inspection focused and efficient.
Training the crew in effective communication is also important. They should know how to present information in a clear, concise manner, which not only demonstrates their competence but also their professionalism. Empowering the crew with communication skills equips them to handle inspections confidently. This training should cover not just verbal communication but also how to present documents and records in an organised way that inspectors will appreciate.
The attitude of crew during these interactions also matters. Approaching the inspection with a cooperative mindset transforms it from a test into an opportunity for improvement. This positive stance encourages a more open and productive dialogue between the crew and the inspectors, potentially turning challenges into learning moments.
“We know the ship’s not going to be perfect. And so one of the first questions is to ask what defects are there on board? And it’s important that there’s real honesty and transparency there because one of the things that really does upset the inspectors is being told that everything’s good, everything’s fine.
And then one thing after another fails to operate or isn’t there, doesn’t work, doesn’t operate as it should do. And that really is a reflection that they haven’t been honest and transparent and that leads that sort of suspicious approach. They told me everything’s okay, but it isn’t’, now I’ve got to question everything.”
– Andy Easdown
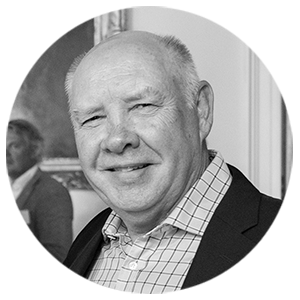
Equipment Checks:
Conducting regular equipment checks and maintaining all onboard systems are part of the day-to-day operation of a vessel, as well as being essential to ensuring a vessel’s readiness for inspections. This process involves:
Scheduled Inspections: Establishing a routine for inspecting equipment means no component is overlooked. Each piece, from navigation tools to safety gear, needs a check-up to confirm its operational integrity.
Proactive Maintenance: Addressing wear and tear before it becomes a significant issue is crucial. This involves replacing parts and correcting any irregularities identified during routine checks.
It can be important to leverage technology to streamline these processes. Planned maintenance systems that bring in data from sensors or observation allow for predictive maintenance, alerting shore teams and crew to potential equipment failures before they occur, allowing for pre-emptive action. These innovations ensure that every piece of equipment is not only functional but also compliant with the latest safety standards.
The crew is responsible for ensuring that equipment is properly maintained and must also be sufficiently prepared to demonstrate proper equipment use to an inspector. Regular drills and hands-on training sessions are important so that each team member is skilled in the use and correct at use and maintenance of the vessel’s equipment. This direct engagement helps develop a deep understanding of the equipment’s functionality and potential failure points, allowing the crew to confidently navigate through the inspection process.
“Things always have to be maintained and looked after. There’s nearly always something which isn’t working. There’s nearly always something which could be better. The reality of crew changes means what was known by one person when they were on board isn’t known by the new person who comes on board.
You mustn’t make assumptions that just because everything seems to be running okay today, that that same level has been maintained all the way through.”
– Andy Easdown
Training for Inspections & Simulating Mock Inspections:
“..a well trained ship is a well run ship and it’s really obvious the people who’ve received training and those that haven’t.”
– Andy Easdown
These sessions are far from dry lectures; they’re interactive discussions that invite the crew to really understand why and how things are done on board. This way, they’re not just following procedures but understanding the reasons behind them, which encourages a proactive stance on safety and compliance. Every crew member, no matter their rank, needs to fully grasp their part in keeping the vessel up to the mark.
Simulations then take this preparedness to the next level, moving from theory to hands-on practice. They replicate the stress and situations of real inspections, providing a practical arena for applying what’s been learned. These exercises are carefully crafted to run through various situations, from emergency responses to everyday checks, ensuring that the crew can confidently handle whatever comes their way.
The role of feedback in this cycle is really important. It’s not just about pointing out errors but about celebrating what went right and understanding how to replicate that success. The moments after a simulation, when you all reflect and discuss, are where true learning happens. This reflective practice means each training session is sharper and more effective than the last, continuously boosting the crew’s skills and self-assurance.
Having your leaders involved in these training and simulation sessions sends a clear message about your collective dedication to being inspection ready. It shows inspectors you’re all in this together, committed to maintaining the highest safety and compliance levels. A united front is crucial when it comes to performing seamlessly during inspections. Plus, it’s a chance for your leaders to mentor and motivate the crew directly, embodying the principle that true leadership involves being part of the journey.
“One of the best possible things that can be done is to use things like toolbox talks. There’s a term that Hayden used when we were chatting the other day, a ‘reverse toolbox talk’, where you can question and actually have that discussion, asking ‘do you think that really is the best way?’, ‘Is that what the procedure says?’, or ‘What could be the safety risks of doing that?’
So, all those things are training actually, they’re not what we perhaps consider formal training, where you sit down in front of computer or perhaps these days on your own device and go through a program, but they are all part of that training process. And the more familiar you become with your operations on board, if you like, the more the training supports what you’re doing, it helps you to get more job satisfaction as well.”
– Andy Easdown
The culmination of consistent training and detailed simulations results in a crew that’s not just reacting when an inspection comes around but is genuinely ready and engaged. This preparation means that when inspectors come on board, they’re met by a team that’s not only knowledgeable and confident but also proficient in showing just how well your vessel meets the highest standards.
Documentation:
Maintaining an organised and up-to-date documentation system is crucial for passing inspections. Documents serve as tangible evidence of a vessel’s compliance with safety standards and regulatory requirements. Ensuring that logs, certificates, and records are meticulously kept not only facilitates a smoother inspection process but also reflects the operational integrity and commitment of the crew. Regular updates and accurate entries in these documents are vital, as they provide a real-time snapshot of the vessel’s adherence to safety protocols.
The transition to digital document management systems is a significant step towards enhancing efficiency and accuracy in documentation practices. This approach minimises the risk of misplacing critical documents and allows for swift retrieval when needed, streamlining the inspection process. The implementation of digital systems ensures that all documentation is backed up, secure, and easily accessible, which is particularly important in high-pressure scenarios that require quick access to specific records.
However, the adoption of digital documentation practices requires regular system audits to ensure ongoing reliability and security. Vigilance in verifying the data in digital systems is essential to maintaining their efficacy, emphasising the importance of periodic checks to safeguard against data loss or discrepancies. Such diligence ensures that the digital documentation system remains an effective tool in demonstrating compliance and upholding the vessel’s readiness for inspections.
“We really want the ship to do well. We want the crew to perform to their best and the key to that is that they’ve done good preparation, they know what inspection is being asked for, they know the areas that the inspector is going to look for, and they have everything ready. They’ve tested it, they’ve tried it, they’ve got the documentation ready, they’re really properly prepared.”
– Andy Easdown
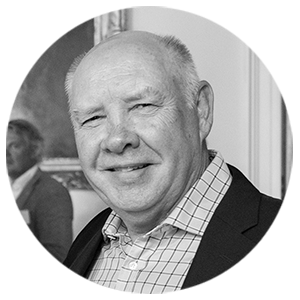
In summary, transparent and cooperative engagement with inspectors is crucial. It involves clear communication, effective listening, and a positive attitude.
The maritime industry’s best e-learning content
Unparalleled breadth and quality of content. We offer the most comprehensive library of maritime blended learning content ever assembled.
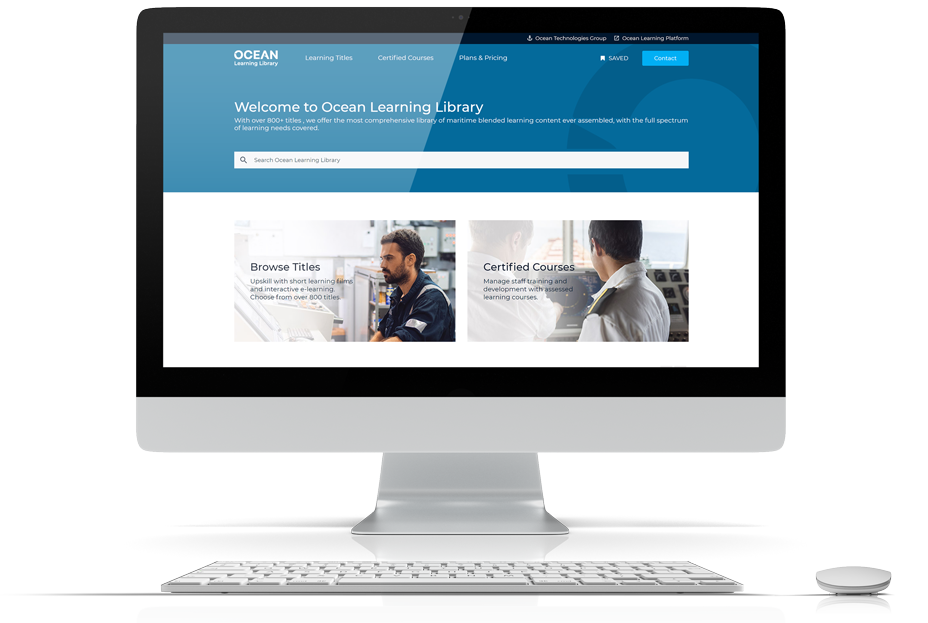