Eliminating the pitfalls of maritime inventory management
Managing inventory for vessels is a complex task that requires careful coordination between multiple stakeholders.
Keeping adequate stock levels while staying within budget is a constant challenge, particularly as supply chain disruptions, regulatory requirements, and sustainability goals add further pressure. Sourcing reliable suppliers who can meet lead times without compromising quality or compliance only compounds these difficulties.
Without a robust system in place, manual processes and disconnected workflows create vulnerabilities that expose businesses to unnecessary risks.
Poor inventory management can lead to shortages that disrupt maintenance schedules, delays that result in costly downtime, and excess stock that ties up capital. These inefficiencies ultimately impact operational reliability and profitability.
Storing all maintenance plans and records in a digital system alongside procurement data reduces the risks of urgent rushes and complications. Procurement teams can independently forecast what stock will be needed in future periods.
This enables them to organise purchases, budgets and spending in advance, according to historical, planned and even real-time maintenance data – without the need to make any emails or phone calls.
Digital solutions provide a smarter way forward, enabling procurement and technical teams to gain full visibility over stock levels, automate reordering, and align inventory with planned maintenance needs.
By connecting procurement, inventory and maintenance management in a single system, companies can ensure safety, improve operational efficiency, and significantly reduce costs.
Stay equipped ahead of vessel maintenance
Marine fleets may be at risk of emergencies caused by delayed maintenance if their purchasers struggle to gain timely access to maintenance records, particularly if they are kept in a separate location. Consequently, rush orders carrying high fees are more likely to incur when urgent parts are found to be out of stock.
Having all maintenance plans and records in a digital system alongside procurement and inventory data reduces the risk of unplanned orders and the costs that come with them. Procurement teams can forecast the stock stock needed for future periods, enabling them to plan budgets and spending in advance.
A digital fleet management solution, such as TM Master, connects procurement and maintenance planning into a single flow. In practice, this means that procurement teams would know what each vessel needs ahead of any maintenance job or requisition, even when changes are made to plans. With a clear view of planned maintenance, Procurement Managers are able to better control costs and ensure the smooth operation of every vessel in a fleet.
Minimise stock levels
Marine procurement teams can waste millions in their annual expenditure on mismanaged inventories. The cost of resolving stockouts or paying for unnecessary storage facilities to store overstocking can quickly add up. Commonly, behind this issue is a lack of visibility over inventory levels and locations, which can lead to both stock shortages and over-ordering.
Using data on past spending on maintenance, teams can predict future needs, then identify ways to limit spending. When accurately collated in a digital system, these insights empower procurement teams to make informed decisions on what items are needed and in what quantities, when, and how often. With this best practice, procurement managers can find opportunities to run lower stock levels, which may also save money on hiring costly storage facilities.
Combining historical consumption data with planned maintenance and up-to-date information on stock levels, companies can plan procurement over longer time frames and calculate long-term budgets accordingly.
TM Master’s Forecast tool gives procurement teams a long-term overview of maintenance jobs, informing them of the total volumes of spares and consumables needed in a given period – including for any upcoming projects or extensive work at drydock. This information can then be used to secure better deals through advanced orders, volume discounts, and competition between suppliers.
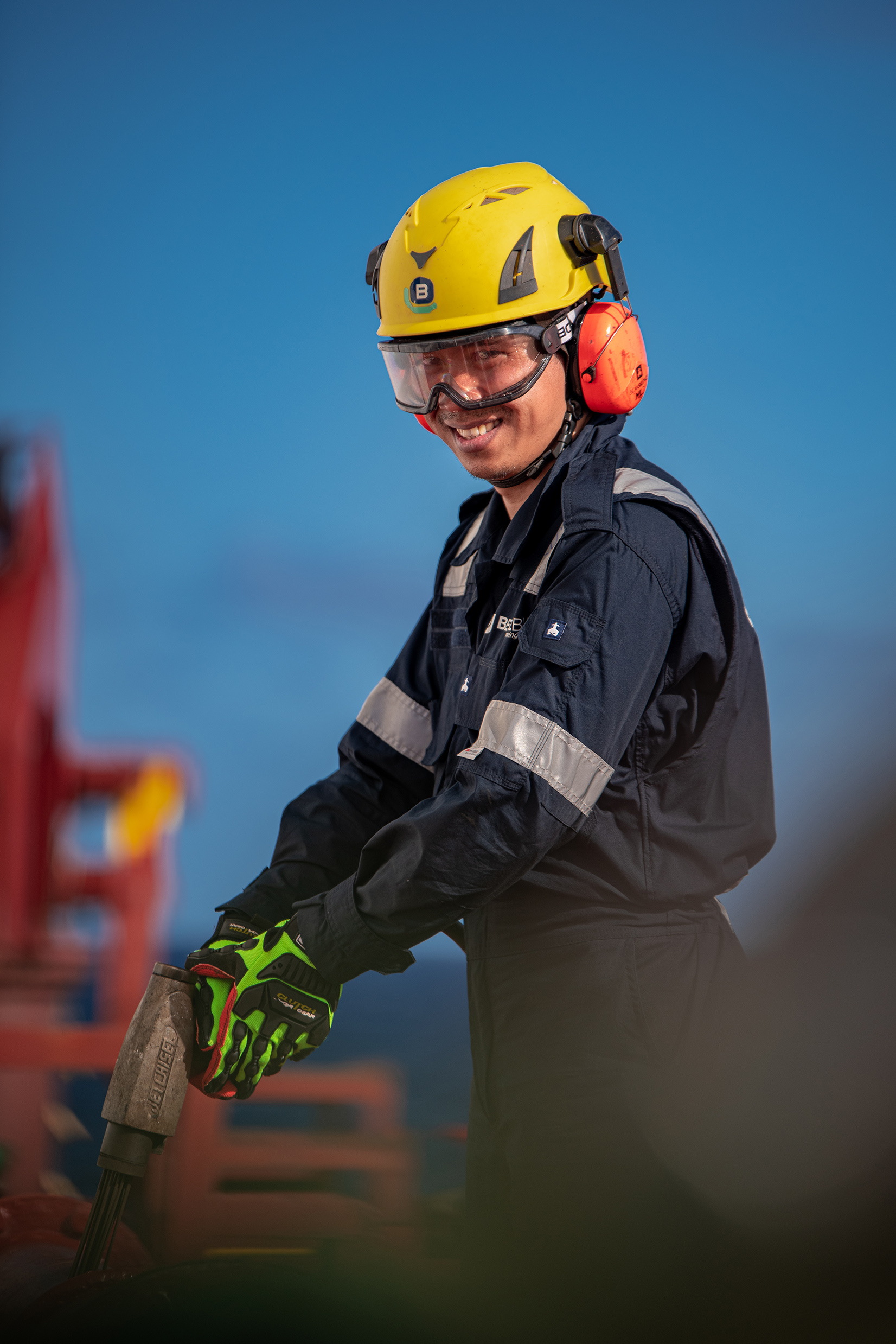
Strengthen connections with reliable suppliers
Keeping track of multiple suppliers is complex, particularly when managing purchasing for a fleet of vessels, each with different equipment, maintenance plans, and ports of call.
Staying on top of communication with suppliers is a constant challenge, with risks of costly delays if responses are missed. Additionally, global trading comes with the challenges of navigating international currencies and shipping costs to understand who is offering you the best deal.
Not all suppliers are equal, with some being more reliable than others – either in quality of service or the quality of what they deliver. Without full visibility of previous buying experiences, it can also be difficult to make the right choice on which supplier to use confidently.
If a supplier has let your company down in the past, you would think twice about using them again in the future. However, with so many purchases being made, quickly assessing which is the best supplier to go with can be challenging.
Maritime procurement teams can use digital procurement systems to centralise correspondence with suppliers, set automated notifications to speed up response times from either party and streamline selecting and assessing multiple suppliers to find the best deals.
Many systems also provide tools to review and track reliability for each supplier on the go, so their quality of service and products can be easily compared at the time of ordering.
As an example, TM Master enables teams to send out RFQs to multiple vendors in one click, integrate with their stock system via an e-commerce platform if necessary, and set up automatic reminder emails to chase for a response.
A built-in price comparison tool enables you to compare supplier quotes side-by-side, converted into a common preset currency that factors in shipping, tax, and any other fees, to provide a true comparison.
Conclusion
Effective inventory management relies on having the most accurate and current information on existing inventory and upcoming needs, combined with confidence in the reliability of your supply chain. Using digital procurement tools is key to easily selecting the best vendors and maintaining strong connections with them.
However, by connecting maintenance and procurement systems, ship managers gain the advantage of a clear view of current and future inventory alongside maintenance needs. This empowers procurement teams to make informed purchasing decisions, ensuring vessels have everything they need without threats to time and budget.
In the long term, by creating a more robust purchasing and maintenance workflow, efficiency is increased, unlocking opportunities to strategically reduce both CapEx and OpEx and increase vessel utilisation.
Learn more about TM Master here
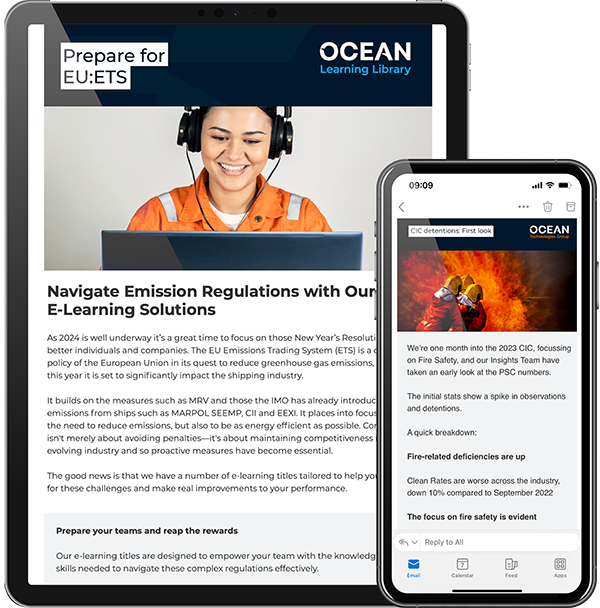
Want to be first to hear all our news?
Subscribe to our Newsletter to keep up to date!
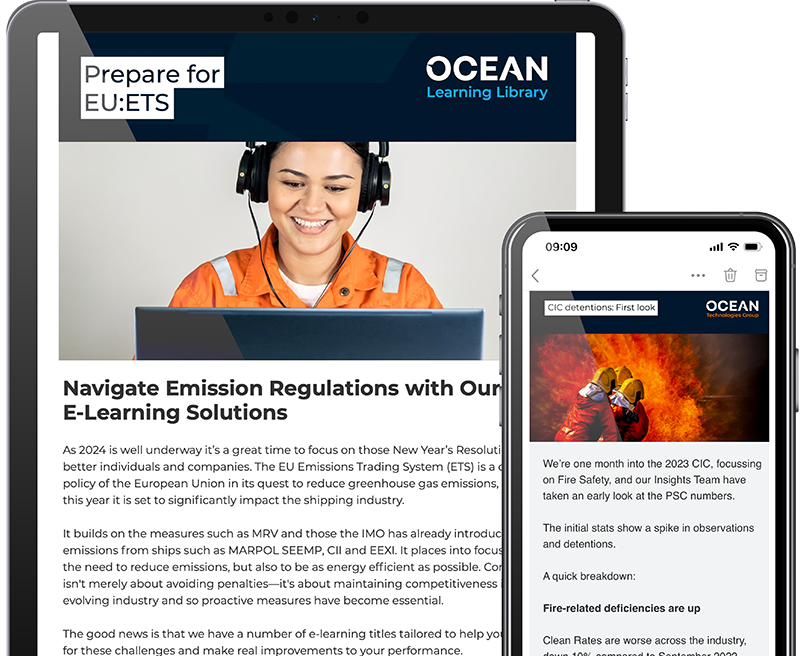