Optimising marine fleet maintenance through digital PMS
Ensuring the safety and operational efficiency of your vessels is non-negotiable. A well-structured maintenance plan is not just a best practice — it’s essential.
Effective planning maximises vessel uptime, enhances Port State Control (PSC) performance, and mitigates the high costs and risks associated with unplanned maintenance. By critically assessing and optimising your current maintenance processes, you can significantly improve both productivity and safety across your fleet.
Yet, some companies still manage maintenance manually, through disconnected systems, or even in Excel spreadsheets. While this might seem convenient and cost-effective, it brings significant risks and inefficiencies that can compromise safety, compliance, and operational performance. Here, we explore these challenges and why transitioning to a digital Planned Maintenance System (PMS) like TM Master is a smarter approach.
The risks of outdated practices
Managing maintenance records manually or in spreadsheets might seem like the best way to have control, but it introduces significant risks and potential complications. Data entry errors, duplicate records and information gaps are common pitfalls of this approach, in addition to the excess time needed to extract and collate information in moments of reference.
Relying on email and phone calls to share maintenance schedules or determine stock quantities can lead to confusion over which version of a document is most recent. This can result in incorrect decisions or delayed actions, which can impact the efficiency of your business. Meanwhile, managing requisition approvals manually can create bottlenecks, delaying essential maintenance or repairs and potentially putting crew safety at risk.
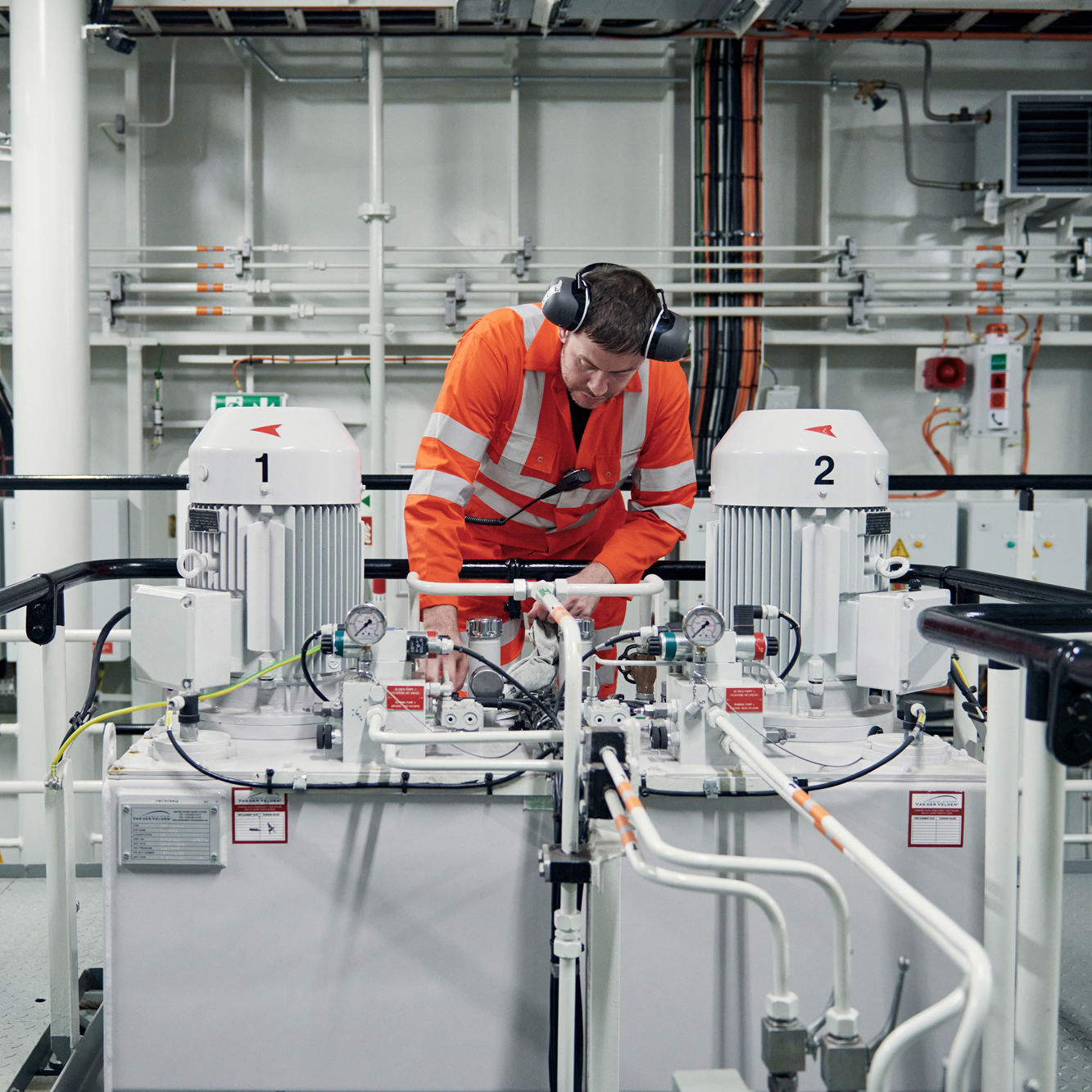
Why work smarter?
Crucially, not having full visibility of your fleet’s condition could have serious implications, especially if you must respond promptly to a technical concern. If any machinery is exhausted or damaged without your knowledge, you could be putting your crew and vessels at risk. This lack of visibility is a significant liability in an industry where safety and compliance are paramount.
Using a digital planned maintenance system (PMS) to centralise your maintenance workflows is a game-changer. The software makes information more accessible and easier to distribute, cutting out time spent searching through documents and inboxes or making email or phone enquiries.
Transitioning to a digital PMS like TM Master centralises all maintenance data in one place, providing clearer visibility of your assets and resources while reducing the risks of downtime, delays, errors, and unnecessary spending. It also enables teams to work smarter to save time, effort, and costs.
Get full visibility of your vessel maintenance
A digital PMS centralises maintenance planning and tracking in one secure place alongside historical records. Any required information is available by quick search, minimising time spent typing emails or picking up the phone. All relevant stakeholders can get visibility of the same information, eliminating the need for calls and emails.
With TM Master, everyone involved in planning, purchasing, and carrying out maintenance has access to accurate information on processes and progress. This enables you and your teams to make informed decisions, respond to any issues quickly, and maximise utilisation.
Have a single source of truth
Accurate records and accurate data are critical to a modern business. Conversely, incomplete or inaccurate data can lead to wasted effort, higher costs, and an increased risk of unplanned downtime to carry out a repair or wait for a part.
Holding information in disconnected silos, such as in spreadsheets, increases the risk of errors or discrepancies. Having an accurate digital record of all your plans and parts in a single system reduces the likelihood of mistakes and the costs associated with rectifying them.
Using a digital PMS provides an up-to-date and easily accessible single source of truth. It eliminates the need to find the most recent version of a file or contact a vessel for an update. TM Master holds an accurate and trustworthy record of the maintenance and performance of equipment and parts across their lifecycle. This gives you a comprehensive picture of maintenance across your fleet and a clear view of any risk. You can then revise and communicate plan alterations based on changing needs or best practices.
Strict rules in a digital PMS act as guard rails to protect the accuracy of your data. TM Master ensures that all data is captured accurately through mandatory fields and controlled user access, minimising the risk of errors and enhancing compliance with regulatory standards. Defined user permissions and version control ensure clarity over when records were updated and by who, as well as the security of being able to roll back to an earlier version in the case of an error.
Reduce inventory spending
Having instant insight into the exact quantities in your inventory enables you to forecast needs accurately and avoid unnecessary stockpiling or last-minute ordering.
The inventory management tools in TM Master help you accurately predict your requirements for spares and consumables, enabling you to hold lower stock levels with the confidence that your needs are covered. This cuts the amount of money tied up in stock and enables you to plan purchases and secure better prices by buying ahead.
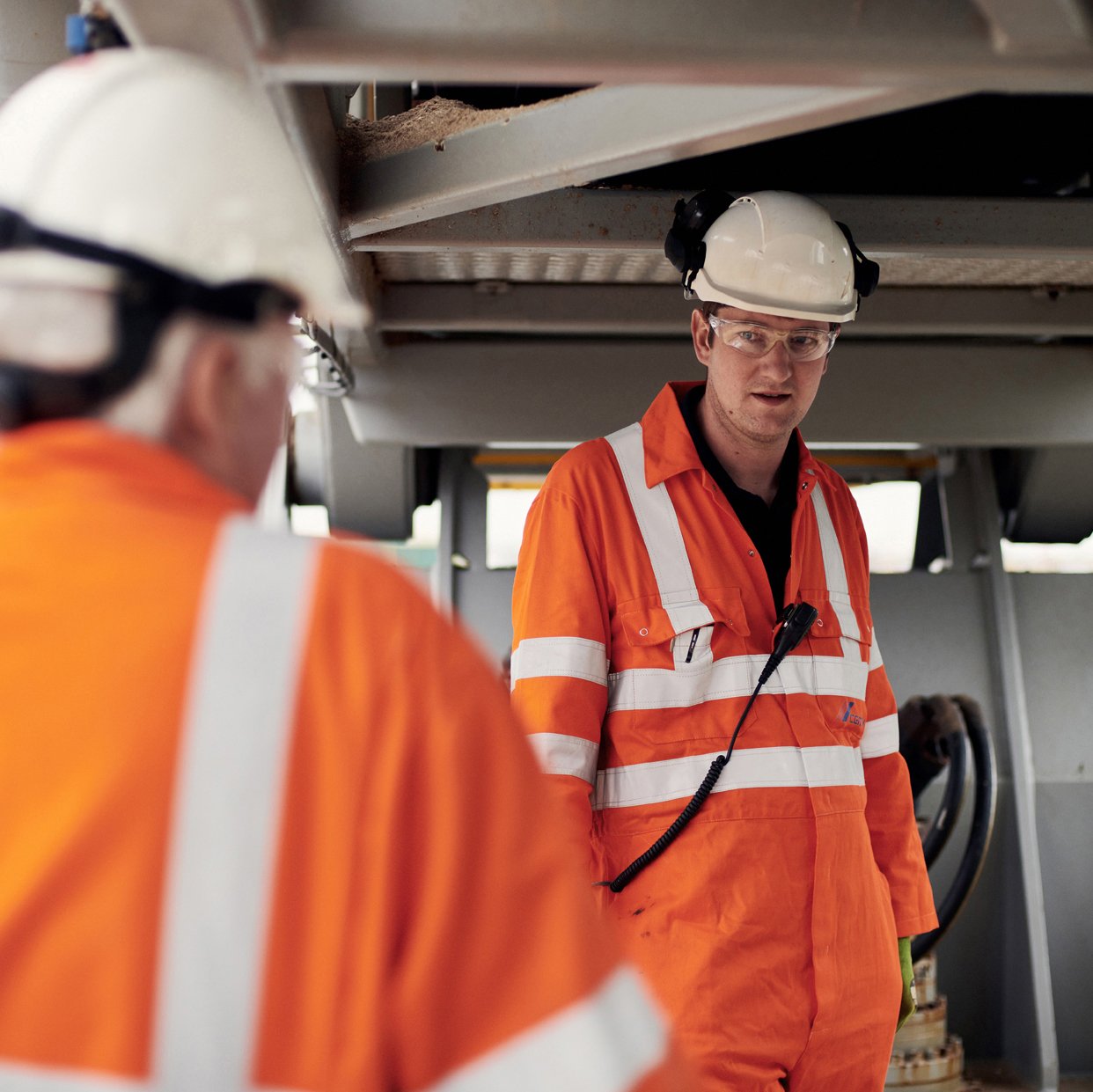
Streamline Approval processes
Delays due to approval bottlenecks for parts or consumables are common. Not having what is needed when it’s needed impacts maintenance schedules, which can have a knock-on impact on vessel performance.
In the case of maintenance, not having a necessary part or consumables can lead to unplanned downtime. However, approvers often have many documents for each request, which can become confusing, especially when they have been shared as attachments in an email thread.
A digital PMS simplifies and accelerates approval processes for maintenance work and parts procurement by reducing effort and the opportunities for miscommunication, which ultimately lead to costly delays. A streamlined system across maintenance and procurement reduces the time needed to create a request for approval, as up-to-date data on inventory, vendor quotes and maintenance invoices can be quickly collated and sent to relevant personnel within the platform.
Utilising TM Master’s automation, you can create rules to remove bottlenecks, including setting up privileges for different users and sending reminders to a contact to respond to an approval request after a given period. The platform also enables you to set value limits for order requests to enable small orders to be processed automatically without approval where necessary.
Have long-term cost control
Managing budgets, ensuring governance over maintenance costs, and keeping spending within set limits can be challenging. Similarly, manually calculating long-term expenditures, such as the overall operational and maintenance costs of a vessel for chartering, dry docking, or insurance, is complex and time-consuming.
With a digital PMS, you can monitor and manage maintenance costs more effectively. TM Master provides long-term projections of cost alongside all your regular maintenance in a single platform. This enables you to routinely assess the cost-effectiveness of your equipment, fleet and processes.
.
In conclusion
In an industry where compliance, safety, and efficiency are paramount, moving to a digital PMS like TM Master can significantly enhance your maintenance operations. Centralising your maintenance processes on a digital platform not only reduces the risk of errors and unnecessary costs but also provides valuable insights for better decision-making and long-term planning.
By adopting a digital PMS, you can ensure that your fleet is maintained to the highest standards, comply with tightening regulations, and ultimately, safeguard your most valuable assets — your crew and your vessels.
Find out more about how TM Master innovates planned maintenance.
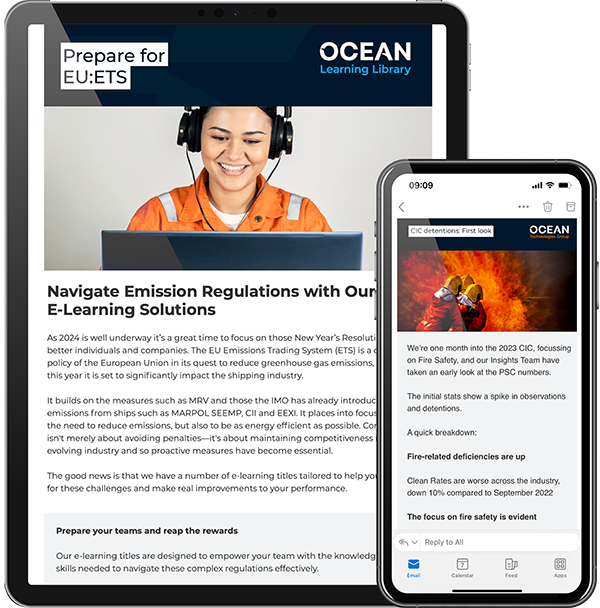
Want to be first to hear all our news?
Subscribe to our Newsletter to keep up to date!
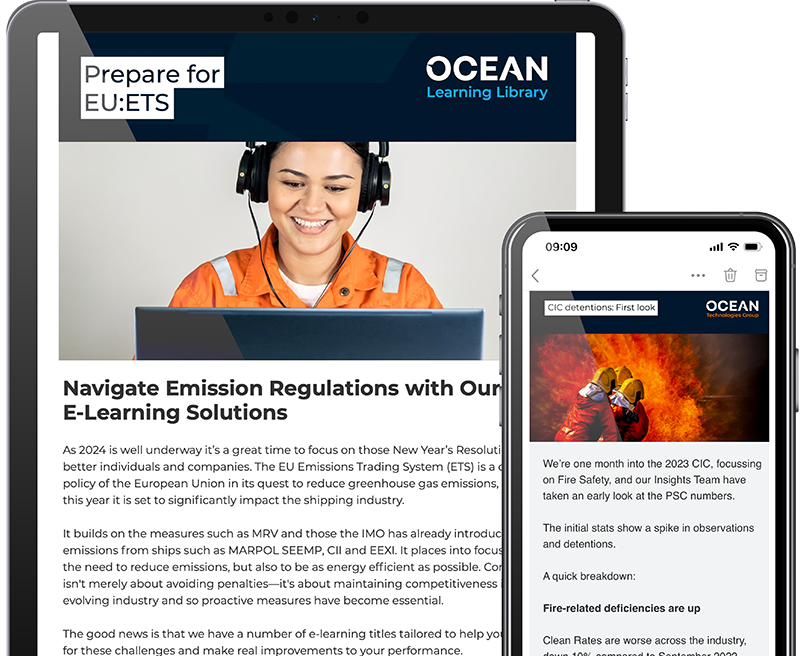